Camshaft (Profile) grinding machine and CAD/CAM Software
Features
TMC Camshaft(Profile) Grinder
- The TMC Camshaft (profile) grinding machine is a CNC grinder that can perform various grinding tasks such as cylindrical, internal, and non-circular grinding required for product processing. Additionally, it allows for quick design and processing of various 3D processing models or CAD drawings by using dedicated CAM software.
- The TMC grinding machine is ready to be adjusted to meet the following equipment specifications for the job requirement:
- - The X and Z-axis working areas, wheel house size, and the selection of steady rest and the number of steady rests structures can be selected to accommodate various types of workpieces.
- - A gantry robot (or multi-joint robot) device can be added to save time and manpower during loading and unloading.
- - By using dressing devices and automatic correction functions, it can increase the life of grinding tools and improve processing quality.
- - Additionally, by adding measuring devices, it can ensure accuracy and quality assurance of workpieces.
MARPOSS
- Using high-precision MARPOSS (or alternative upon customer request) ensures high reliability.
- When using measuring devices, important characteristics of the product such as the journal outer diameter, Cam-base circle, nose, and lift can be measured in real-time, and the measured data can be saved.
TMC CAM - Camshaft Software
-
- TMC CAM - Camshaft allows for the loading of shape information data files for cylindrical, non-cylindrical, and camshaft shapes, or the import of 3D modeling files or CAD drawings, enabling fast processing. The software also includes a shape information generator and editor that allows for the design of new products, and automatically generates the required G CODE in formats such as FANUC, Siemens, etc., for final grinding.
- TMC CAM - Camshaft has an easy-to-use interface and provides intuitive 2D shape and 3D modeling functions. The software includes a processing simulation function that allows for the verification of product design before processing, minimizing processing errors, and the shape information editor allows for quick response to any necessary modifications..
- In addition, TMC CAM - Camshaft allows for more efficient and faster machining by adding multiple stages of detailed cutting conditions.
- - Different grinding wheels can be selected for each stage to reduce rough and finish grinding time.
- - Feed rate, depth of cut per revolution, grinding speed, spark-out cycles, etc. can be set for each stage.
- - The shape profile can be machined smoothly using the Cubic-Spline surface processing method, and when generating G code, the division angle can be subdivided up to 0.01 degrees.
- The cutting speed can be set for each part such as the base circle, lift, nose, and inflection point, and a higher quality product can be machined using the provided automatic calculation function.
- - By reading the dressing status and wheel data of the grinding wheel in real time through network connection, and generating G code, unnecessary machining time is minimized and the quality of the product is improved.
The expectations and benefits of ours
- - Improved productivity and accuracy of product design.
- - Reduction in time from prototype conception to production and shortened Tact-Time of the product, maximizing cost-effectiveness and timely-efficiency.
- - Ability to produce high precision and high-quality products.
- - Possibility of converting manual grinding machines to CNC shape grinding machines with minimal cost by overhauling and equipping them with out CAM software.
Testing Video
Application Case
FANUC SYSTEM
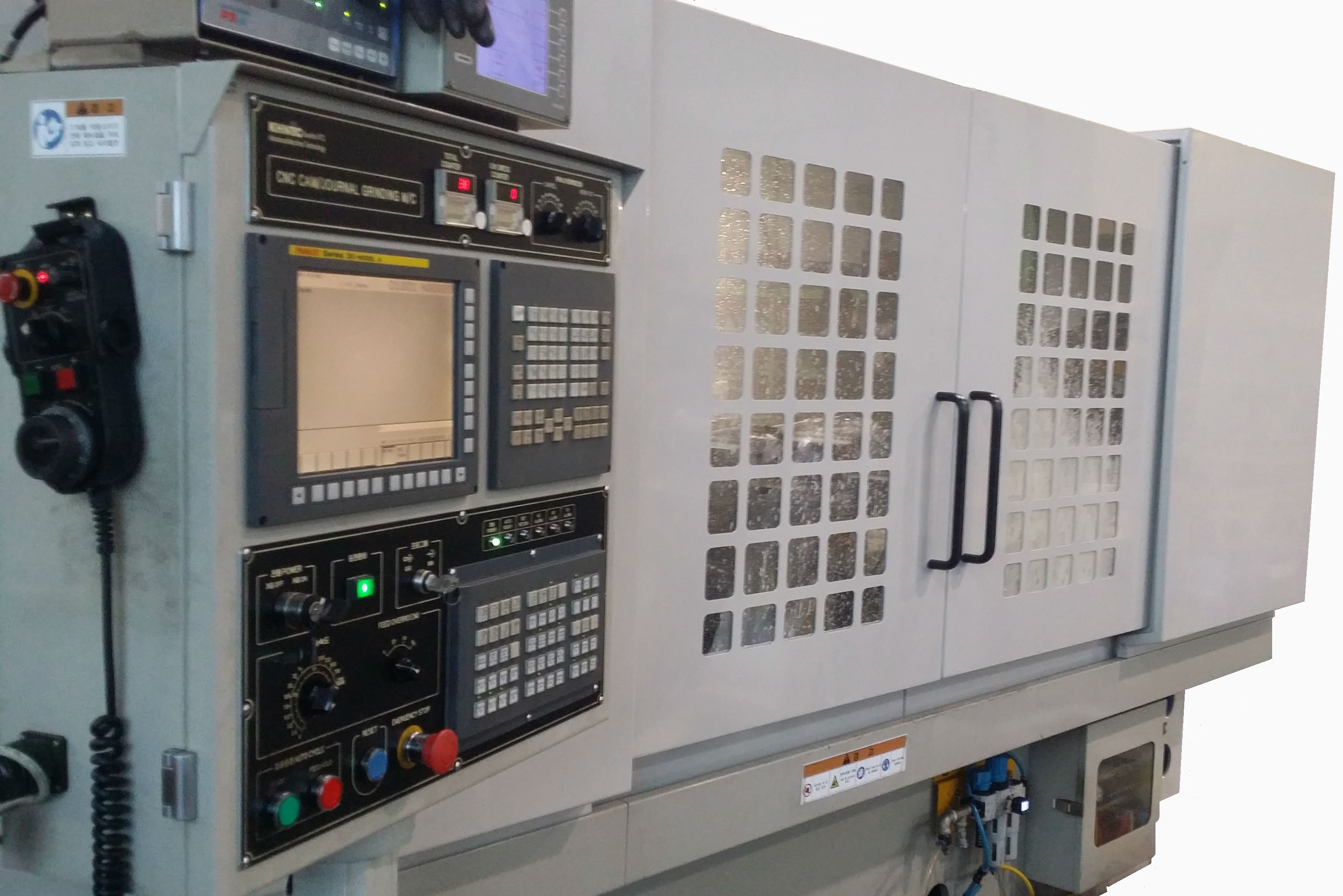
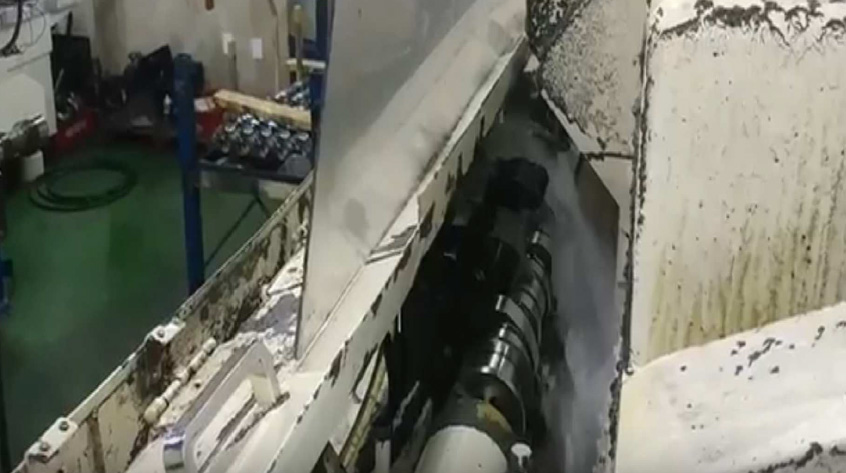
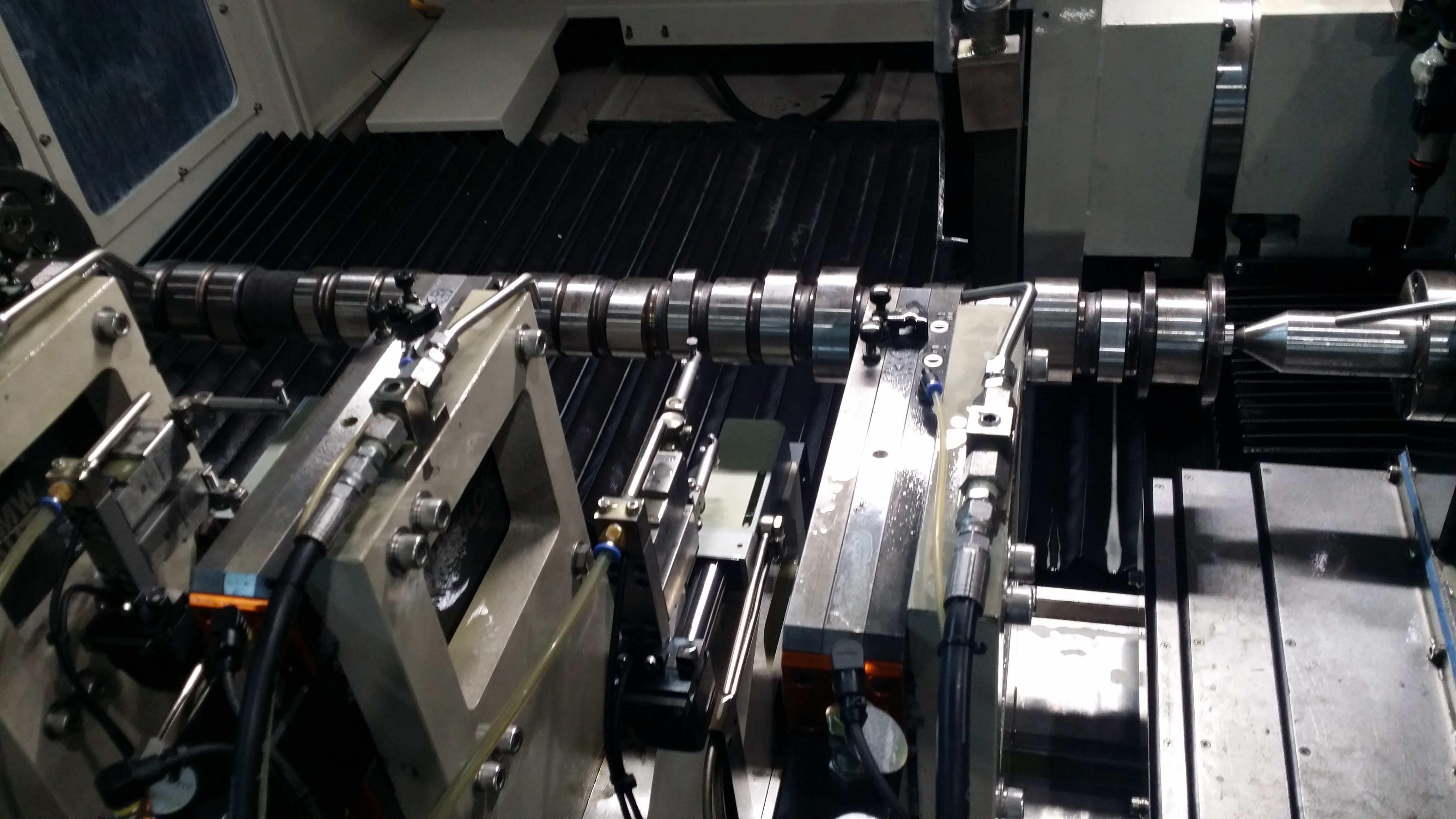
Siemens SYSTEM Studer Grinder
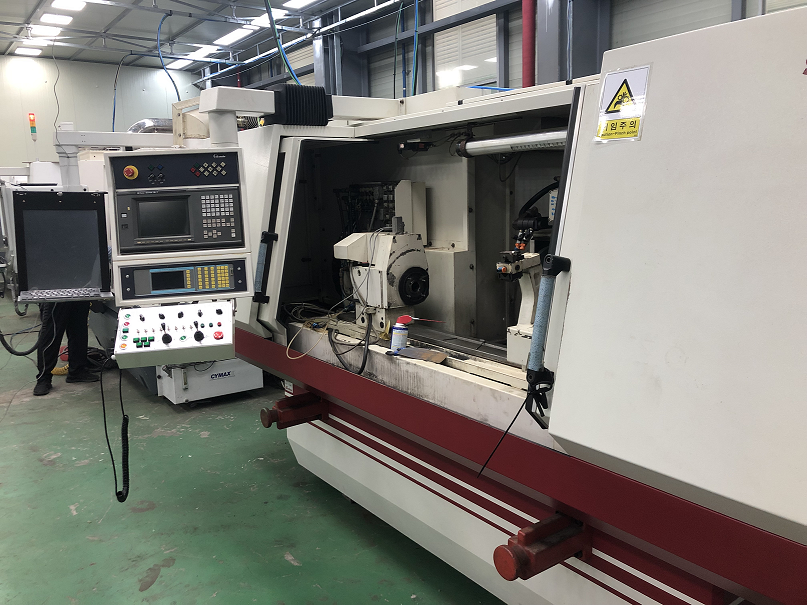
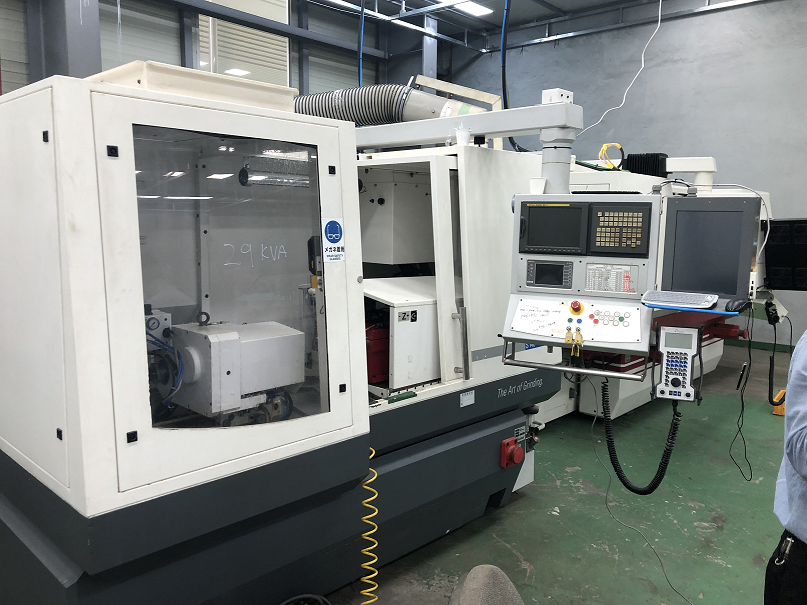
Gearbox Flange Inner Diameter Grinding
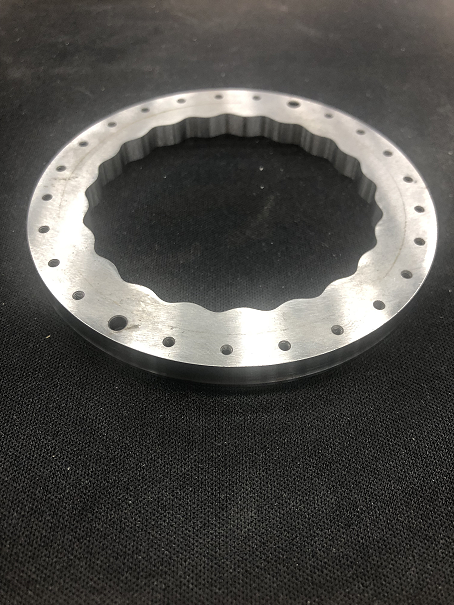
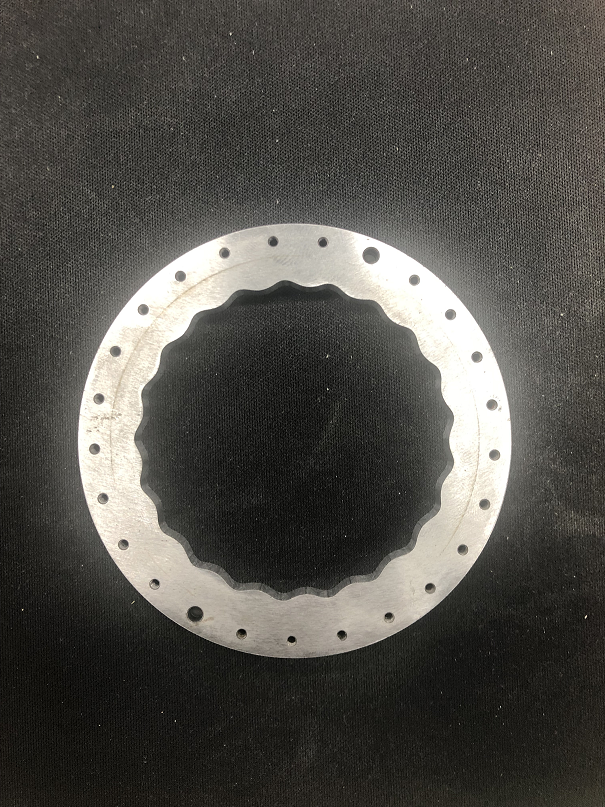